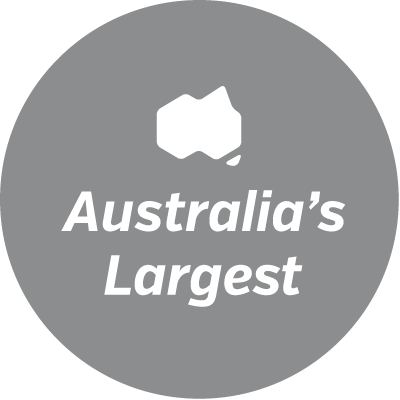
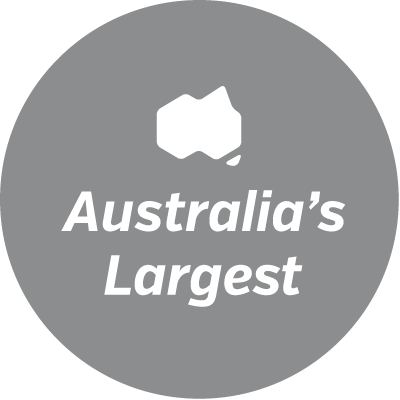
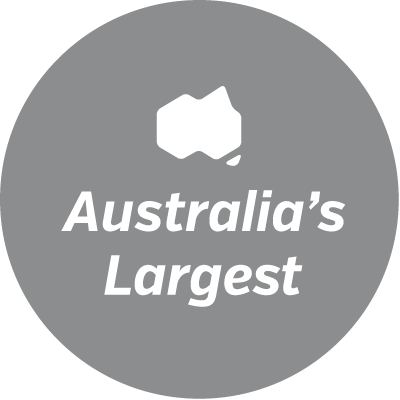
Steel Slitting Line Process
Our high speed slitting line is big – the largest of its type in Australia – but it’s not just size that makes this machine special, it’s the broad range of capabilities it possesses.
Big capabilities
The ability to break down larger coils into smaller ones and the option of applying PE to either the top, bottom or both sides of the material, produces far superior products and sets this machine apart from the rest of the Australian market. Our slitting services are used for solutions such as spiral welded tubes, cable trays, and tube and pipe clamps.
Download BrochureTechnical Specs
Minimum | Maximum | |
---|---|---|
Entry Coil Weight | 2,000kgs | 13,600kgs |
Entry Coil ID | 483mm | 635mm |
Coil Diameter | N/A | 1905mm |
Thickness | 0.5mm | 8.0mm |
Coil Width | 305mm | 2210mm |
Slit Width | 20mm | 2100mm |
Exit Coil Weight | 13,600kgs | 13,600kgs |
Exit Coil ID | 508mm | 508mm |
Accuracy: +/- 0.051mm, Tooling: ASKO Edgemaster shimless tooling,
PE Coating available top and bottom.
Three Stages of High Speed Accuracy
Stage 1
Mandrel and automatic coil tracking system
- Mandrel drives the material along the line, to the tension stand.
- Automatic coil tracking system compensates when the strip deviates from the centreline by moving in the opposite direction until the coil is centred again.
- Material is then sent to the crop shear for initial square edge.
Stage 2
Slitting head
- Traversing base allows the slitter to “float” with the strip while running. This side to side adjustment is motorised.
- System prevents additional camber from being introduced into the slit strips.
- Slitter features:
- Fully automatic pass line compensation
- Automatically adjusts to different knife diameters
- Compensates for material thickness
- PE coating ability for both sides.
- Scrap choppers cut the edge trim and conveyor system carries the scrap to bin.
Stage 3
Tension system, exit crop shear and recoiler
- Automatic tension system assures proper winding tension.
- Exit crop shear cuts the coil ahead of recoiler to eliminate the need for rethreading the entire line when breaking down coils.
- Mandrel gripper compensates for thickness variations across the width of the strip.
- Recoiler tail hold-downs and controls strips, which prevents loose tails at the end of the run.
Frequently Asked Questions
What is a Slitting Line?
A slitting line is an industrial machine that converts large wide steel coils into narrower coils or bands. This allows for more effective stock control and less waste of material for the customer by supplying the required width in bands or coils. specialised band or coil widths are used across many industries, including water, automotive, construction, heavy engineering and appliance manufacturing. A slitting line involves the following steps:
- Uncoiling stock material – feeding the metal coil into the slitting line
- Shearing/slitting – cutting the metal coil into narrower strips or bands
- Re-coiling – winding the narrow strips back into coil form
How Does a Slitter Work?
Slitters use sets of circular knives to cut the coil along its length. These knives rotate on an arbour, with each cutting position creating a slit that narrows the steel’s width. The process is highly efficient and cost effective for manufacturers to reduce material waste.
What is the Slitting Process?
The slitting process begins with feeding the coil into a set of uncoiler arms. These arms hold it in place during feeding. It is followed by a series of straighteners and feeders that drive the material into the slitter for cutting. After that comes a series of tensioning rollers and recoil arms, these rewind the slit material onto new coils for further processing or shipment directly to customers.
How Many Types of Slitting Machines Are There?
There are two main types of steel slitting lines: single-blade and double-blade. Single-blade slit machines have a single arbour that runs the entire line length. Double-blade slit machines use two separate arbours for greater flexibility and speed when cutting.
Single-blade slit machines are typically used for long production runs with few material changes. Double-blade slit machines are ideal for short runs with frequent material changes. Depending on your production needs, you can choose the best system for your process.