Precision Plasma Cutting Steel
Midway Metals boasts Australia’s largest capacity for plasma cut plate processing used by medium to heavy manufacturing, tank manufacturers, water treatment, through to the mining industry.
Our high definition plasma cutting technology is capable of cutting stainless steel from 2mm to 80mm in thickness. All machines are networked using the latest Hypertherm Pronest Computer software, with full nesting facilities including standard development of cones, square to rounds and Lobster Back bends.
Plasma cutting technology uses the fourth state of matter, plasma, to transfer energy from a power supply to any conductive material. Plasma is formed when heat levels are increased on a gas (steam) so that the gases that make up the steam become ionised and electrically conductive. Using plasma this way results in a cleaner and faster cutting process.
Our high definition plasma cutting system is designed and engineered to produce the sharpest, highest-quality cuts possible using plasma. The torch and consumable designs are more complex than that of a conventional plasma system, with additional pieces included to further constrict and shape the arc. It utilises multiple gases such as oxygen, high purity air, nitrogen, and a hydrogen/argon/nitrogen mixture for optimum results on a multitude of conductive materials.



Versatility
Cuts a variety of widths and lengths
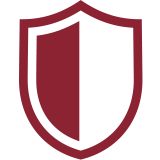
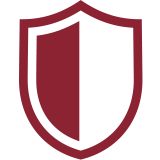
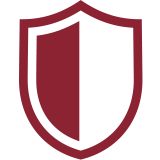
Strength
Large profiles are supplied in one piece for greater structural strength
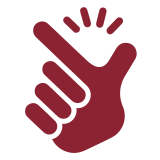
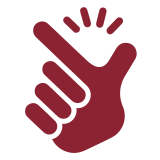
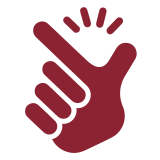
Ease
DXF files can be supplied by email
At Midway Metals we are proudly enabling Australian industries to deliver these world-class products and projects through high-performance stainless steel. We are fully Australian owned and operated and pride ourselves on being the preferred choice for local manufacturers and businesses who need top-quality stainless steel that is fit for purpose and professionally processed. Contact us to talk about your stainless steel needs and how we can help your business or project shine utilising high definition plasma cutting or any of our other stainless steel processes.
Frequently Asked Questions
What is Plasma Cutting?
Plasma cutting (also known as plasma arc cutting) is a melting process in which an accelerated jet of hot plasma is used to cut through electrically conducting materials.
An electrode and workpiece come into contact with an electric arc during the process. The narrow, high-temperature, high-velocity plasma jet is formed when the arc is constrained by the electrode, which is recessed in a water or air-cooled gas nozzle.
How Does Plasma Cutting Work?
Plasma cutting works by sending pressurised gas, such as oxygen, argon, or nitrogen, via a narrow channel. An electrode that is negatively charged sits in the middle of this channel. The connection forms a circuit when the negative electrode is powered up and the nozzle tip is in contact with metal.
The electrode and metal produce an intense spark. This spark heats the inert gas as it moves through the channel, causing it to achieve the fourth state of matter.
This reaction turns metal into molten slag. It produces a directed plasma stream around 30,000 F (16,649 C) in temperature. The plasma stream travels at 20,000 feet per second (6,096 m/sec).
What Sort of Work is Plasma Cutting Used for?
Plasma cutting is frequently used in fabrication shops, automotive repair and restoration, commercial building projects, and salvage and scrapping activities.
How Thick Can a Plasma Cutter Cut Through?
The maximum metal thickness that a typical hand-held plasma cutting device can cut is around 1 inch.
What is the Difference Between Laser and Plasma Cutting?
Although lasers often rely on the power of optical light, plasmas typically use compressed gas to cut. Plasma is exclusively used to cut metal, but lasers can cut various materials.